Supply Chain
- Accueil
- Expertises
- Supply Chain
Nos convictions
Notre expertise
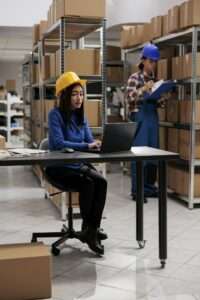
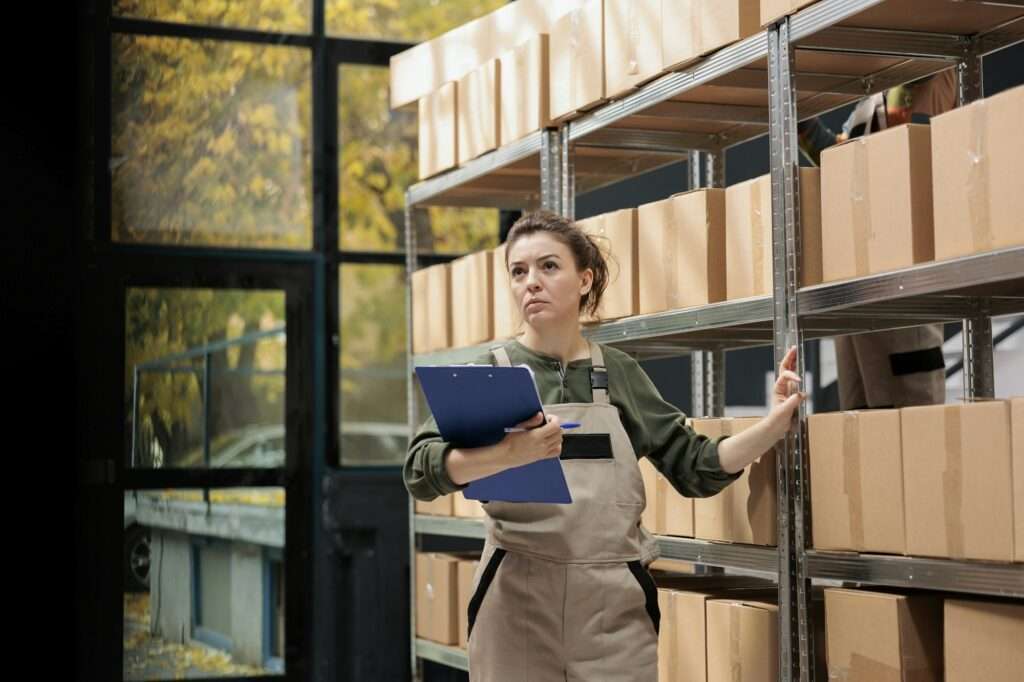
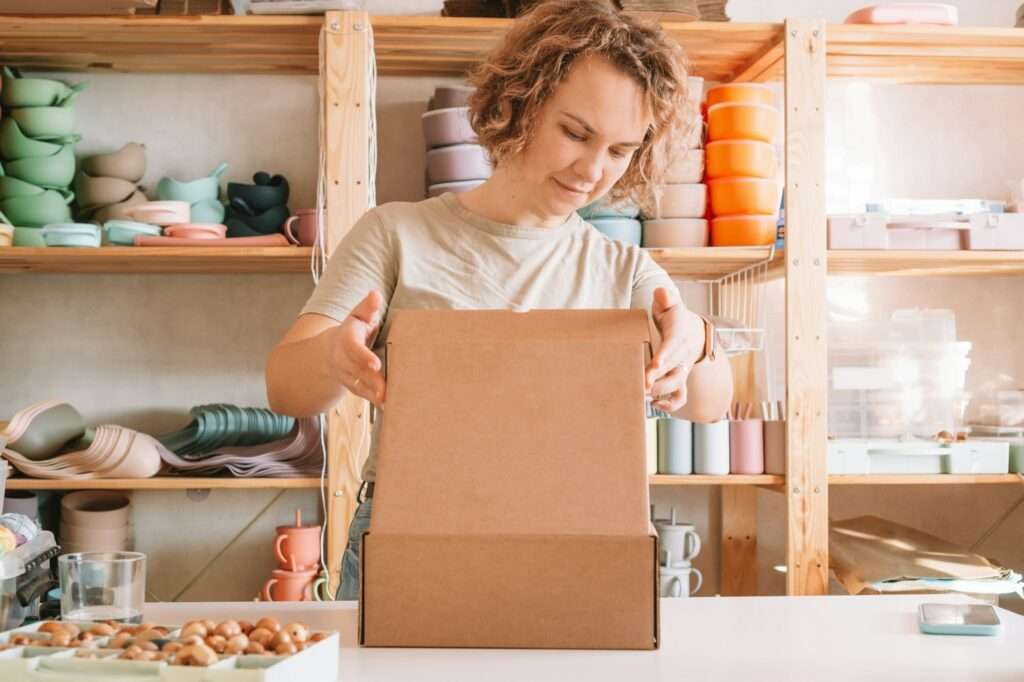
Nos savoir-faire
Planification de la demande
- Organiser et préparer les données
- Élaborer une prévision préliminaire
- Intégrer les données du marché
- Rapprocher des prévisions ascendantes et descendantes
- Élaborer une prévision finale
- Superviser les performances du projet
Gestion des approvisionnements
- Analyser les différentes méthodes d’approvisionnement à appliquer
- Analyser les stocks
- Mettre en place et piloter les KPI
- Piloter les projets visant à optimiser la fonction approvisionnement
- Mettre en place avec les fournisseurs des plans d’amélioration coût/qualité/délais
- Optimiser le modèle logistique
Transport et logistique
- Piloter l’implémentation d’outils de gestion du transport et de la logistique (OMS, TMS, WMS)
- Benchmark solutions du marché
- Manager de transition opérationnel
- Audit de productivité
Amélioration continue
- Certification Lean Management
- Piloter une démarche d’amélioration continue
- Coaching équipes opérationnelles à la démarche Lean
Gestion de projet et conduite du changement
- Cadrer et piloter les projets
- Accompagner aux appels d’offre
- Accompagner au changement
Efficacité
- Excellence Opérationnelle, Amélioration Continue (Certification Lean)
- Organiser la Gestion des Flux
- Gérer les stocks et les Approvisionnements (CPIM)
Utilisation des technologies
- Implémenter les outils de gestion Supply Chain (ERP, OMS, TMS, WMS)
- Benchmark solutions du marché
- Accompagner au choix de la solution
Suivi et traçabilité
- Élaborer des processus de traçabilité et de rappels
- Benchmark des solutions du marché répondant aux normes et réglementations
- RFID
Maximisez l’efficacité de votre Supply Chain grâce à notre Baromètre innovant
Notre Baromètre Supply Chain vous offre une analyse complète de votre organisation logistique en 9 points clés, incluant :
- Vision 360° de votre Supply Chain
- Évaluation de la performance et alignement stratégique
- Optimisation de la satisfaction client et intégration des pratiques RSE
Grâce à des échanges avec les acteurs concernés et l’analyse de données précises, vous obtiendrez des recommandations concrètes pour améliorer votre performance.
Le baromètre se déroule sur 10 semaines avec un investissement de 4 à 5 heures par acteur concerné pour un baromètre complet et personnalisé.
Nos retours d'expériences
Acteur de la distribution BtoB multicanale en Europe
Leader européen spécialisée dans la vente à distance de produits, fournitures et équipements d’emballage
Acteur de la distribution BtoB multicanale en Europe
Témoignage
Aurélien Médina
IT Program Director de Manutan Group
“L’accompagnement d’Univers Retail : professionnalisme car Univers Retail a complétement répondu à mes attentes & intégrité car la solution du nouveau WMS a été choisi pour répondre aux besoins de Manutant et n’a pas été orienté par Univers Retail”